BCP: How do you prepare for typhoons and storms etc. on the logistic workplace? And what is the social responsibility of logistics?
April 21, 2020
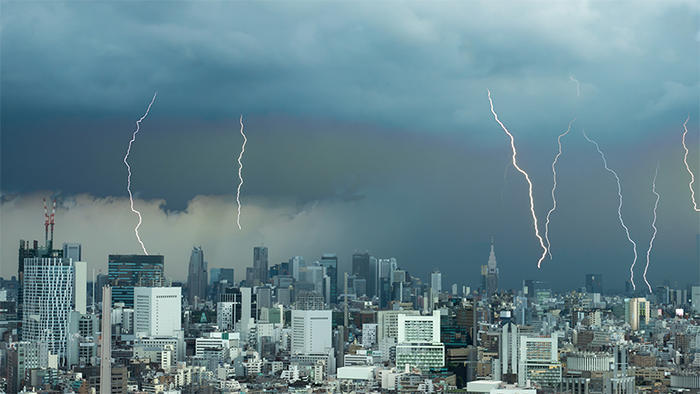
Like coronavirus, typhoons, heavy rains, and flood damage have a great impact on corporate economic activities and people's lives. In the last few years, a number of typhoons, storm rainfalls, and floods have hit Japan frequently, such as the Heavy Rain Event of July 2018, Typhoon No. 21 and No. 24 in September 2019, Typhoon No. 15 in September 2019, and No. 19 and No. 20 in October 2019. These natural disasters have had profound effects on corporate economic activities, including logistics, and people's lives. Although damages and injuries were not as much as that of the Great East Japan Earthquake in 2011, the importance of addressing disaster risks was once again recognised.
Typhoons, torrential rains, floods, etc. are said to be disasters that can be predicted in advance to some extent, therefore taking appropriate disaster prevention and mitigation measures in advance can reduce the damage itself and the burden of business restoration work. Recognising the necessity of such proactive preparations, each company needs to promote initiatives for business continuity, in the form of Business Continuity Plan, or BCP in short. In this article, some tips from Japanese Logistics Service Providers (LSPs) on their mitigation measures against natural disasters and case examples of Nippon Express in relief supplies warehouse operations are introduced.
Flood damage mitigation measures
- Raise the floor level, to prevent damages from water immersion. Where this is not ready, add one to three pallets to heighten palletised cargo or evacuate cargo to higher places using nestainer racks, etc.
- In warehouses, sort things that are likely to be damaged, stack sandbags or install tide plates in front of doors, shutters, underground parking, etc.
- Assuming that the roof may break or be blown off, cover the cargo with blue plastic sheet inside the warehouse even if there is a roof.
- Introduce mobile power vehicles and large drainage pumps and shelter the power supply facilities of the drainage pumps in order to prevent the loss of power in case of flooding.
Wind damage mitigation measures
- Cover around shutters with trucks as a wind protection measures.
- Stack pallets or place forklifts to support the shutter from the inside.
- For ocean containers, stack up to two tiers or lower before the typhoon arrives.
Evacuation of vehicles and equipment
- Evacuate trucks and cargo handling equipment as much as possible to higher or safer place.
- Move vehicles to the rooftops in facilities with a rooftop parking area. For facilities without a rooftop, determine the evacuation location of vehicles based on the risk of inundation around the facility, and decide where to evacuate outside the facilities and negotiate with the evacuation site owner if necessary.
When to start preparing disaster countermeasures?
- Approximately one week before the typhoon landing, start preparing for sandbags, considering evacuation of forklifts and vehicles and adjusting employees' working shifts.
- For a predictable disaster, set up a headquarters for disaster control 72 hours before and commence consideration of countermeasures.
It is important to know the risks of your own facility beforehand from hazard maps etc., and then take appropriate measures to mitigate damages from natural disasters.
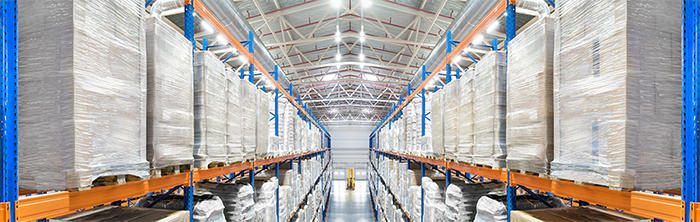
Case examples from Nippon Express:
warehouse operations of relief supplies to disaster-stricken areas
In the logistics industry, not to mention the continuation of its own business, social responsibility for social infrastructure and, in an emergency, social contribution to play a part in the supply system of relief goods are also required. These include disaster agreements with designated public institutions of the Cabinet Office of Japan, local governments, etc.
Nippon Express operated the relief supplies transportation hub in Nagano Prefecture when Typhoon No. 19 hit Japan in October 2019, at the request of the Nagano Trucking Association. The typhoon was born in the Mariana Islands on 6th October, 2019 and brought record-heavy rainfall in the Kanto-Koshinetsu and Tohoku regions. More than 900 people were forced to live in shelters.
At the transportation hub, Nippon Express operated the warehouse operations, picking and sorting of relief supplies. They were also in charge of the warehousing and shipping of donated items, including home appliances donated from Nagano prefecture, to 600 of affected households by January 2020.
It was worthwhile to make full use of the business know-how of logistics centre operations as well as strengthened cooperation with Nagano Prefecture and Nagano City.
As another case example, Nippon Express was one of the companies that carried out the alternative transportation of railway containers that were suspended during the Heavy Rain Event of July 2018. The operations include arrangement of vehicles, drivers, parking lots and accommodation facilities, and carrying out a series of schedule planning and operation management. Nippon Express also took part in the alternative transportation by ocean transportation as well. Nippon Express has handled approximately 9,300 containers by trucks and 6,500 by ocean, which is a total of approximately 15,800 containers, as an alternative transportation for railways until the resumption of all Sanyo Lines on September 30th 2018.
In this way, logistics has a significant social role as a lifeline that protects the lives and daily lives of people, including disaster victims.
Reference:
- Japan Association for Logistics and Transport: Guidelines for creating a BCP (Business Continuity Plan) for the logistics industry in the event of natural disasters version 2.0, 2020 (Japanese version only)